Stained-glass windows: a variety of types, stained glass techniques and their scope
Content:
- Classic stained glass window
- Tiffany
- Fusing
- Sandblast
- Painted
- Film
- Jellied
What is a stained glass window? This concept includes a fairly wide range of various ways to decorate surfaces such as glass or mirror. The unique properties of these materials imply various methods of processing them, which are used both individually and by mixing or combining different techniques.
Types of stained glass technologies
Fusing
Fill Stained Glass
Painted stained glass
Matting
Film Stained Glass
Sandblast
Classic (or typesetting)
Tiffany
Combined Stained Glass
Faceted Stained Glass
Photo printing
Cast Stained Glass
3D stained glass
Let's consider in more detail each type of equipment separately
Classic stained glass window
The classic (typesetting) stained-glass window is one of the oldest ways of decorating, because It originated in the Middle Ages. This technique was used mainly in church buildings, temples and cathedrals. Nowadays, preserved classical stained-glass windows on the windows can be seen if you visit ancient castles, temples, as well as European estates. Today, the technology has remained the same, however, in combination with new materials and tools.
The manufacturing process of a classic stained glass window consists of several stages:
- a sketch is made;
- in accordance with the sketch, a pattern of a metal profile is laid out;
- cut glass parts are inserted into the profile, while the joints are welded together;
- Further, the process of painting the stained-glass window is carried out.
For the manufacture of the metal profile, metals such as copper, lead and brass are used. In cross-section, the profile resembles the letter H, and therefore it is called H-shaped. Colored glass elements are installed in the lower and upper grooves of this profile. At the joints, the glass parts are welded together, thus reliably fixing the parts relative to the broach. This technology allows you to hold glass having a thickness of up to 4 mm, thus being sufficiently reliable. But at the same time, the technology of the classic stained-glass window has its minus - a rigid profile does not provide the opportunity to create soft curved contours of the image. Medieval craftsmen used only a lead profile for stained glass, which also has a number of its drawbacks, for example, it is quite soft and fragile. Among other things, having a very large width (4 - 6 mm), it does not meet the requirements for grace of seams. In this regard, in modern times, the lead profile is used primarily for the restoration of ancient stained glass windows.
Multi-colored glasses represent the basis of the classic stained-glass window, on which not only the aesthetic appearance, but also the light transmission depends. Nowadays, there is a huge variety in the choice of stained glass. But glasses of such brands as Glashutte Lamberts, Spectrum, Wissmach ,, Armstrong, Uroboros, which do not fade, are considered to be the best quality, representing glass painted in bulk, and not using single-sided painting or film application.
The classic stained-glass window technique is optimal for large-sized stained-glass windows.
Tiffany
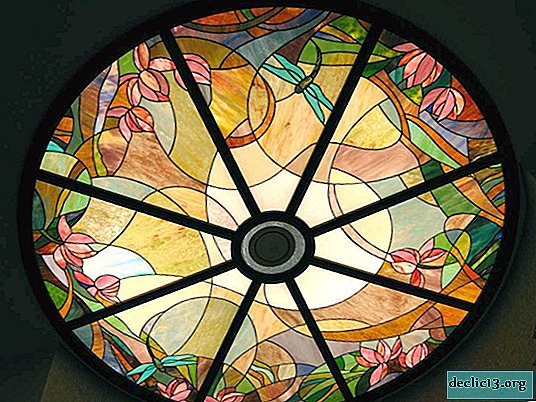
The Tiffany technique is named after its creator and founder Louis Comfort Tiffany, who for the first time in the late 19th century created opal glass with unusual aesthetic properties. The unusual inner light of the glass and the rich variety of shades simply amazed the imagination. Currently, this technique has gained immense popularity and demand due to its high aesthetic and artistic qualities. Tiffany's stained-glass windows are distinguished by extraordinary realistic images and “liveliness” of the graphics of created images, which is achieved by using even the smallest glasses, as well as convex and concave. In general, Tiffany's stained-glass windows from an artistic point of view are comparable to paintings made on canvas, and represent real works of art. It should be noted that the technique is almost entirely based on the manual assembly method, being the real author's work. Each stained glass window is truly unique and individual, because a second time it is exactly impossible to repeat even to the most experienced professional master. The process of creating Tiffany stained glass windows consists of several stages:
- a sketch is created;
- the sketch is divided into several fragments;
- stained glass details are cut out of glass;
- glass fragments are machined on a special machine to give the desired shape and size;
- each glass element is wrapped with copper duct tape;
- parts are connected to each other using lead-tin solder.
Unlike classic stained glass windows, Tiffany stained glass windows do not use guide profiles. The technology also allows you to use even the smallest details, which gives stained glass the incredible complexity of the composition being created. Seams have different thicknesses, which undoubtedly emphasizes the fact that the mosaic is handmade and is exclusive and unique. Particularly thin seams are achieved by applying special paint, which is applied at the joints of glass elements. The copper base, unlike the lead base, allows fastening parts at different angles, creating the effect of volumetric and convex stained glass images. Among other things, the stained-glass windows using the Tiffany technique are very resistant to extremes of high temperatures and external influences. Despite the fact that the stained-glass windows consist of individual glass fragments, they are not inferior in strength to products from a single piece of canvas.
Fusing
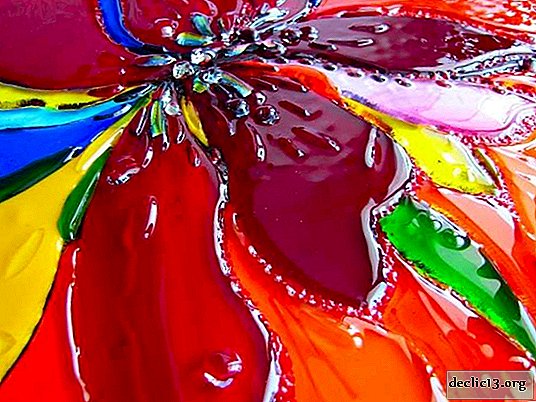
Fusing technique provides the opportunity to create unique highly artistic compositions that will become a worthy decoration of the interior. The process is based on the sintering of glass parts in a special fusing furnace. In the modern world, technology has appeared relatively recently, however, it has existed since ancient times, because archaeologists have discovered the remains of fusing products in the tombs of the pharaohs. The technology also includes several stages:
- sketch design;
- cutting glass parts according to the sketch;
- collection of glass blanks;
- sintering process.
A glass base is laid on a flat surface on which a pattern of pre-cut multi-colored glass elements is laid out in accordance with the developed sketch. In order for the glass fragments to hold firmly, a special glue is used, which fixes them to the glass-based. When creating a thick fusing product, a second glass base is used, which closes the assembled pattern, thus forming a “sandwich”.
The sintering process can also be divided into several stages:
- Slow heating, starting from room temperature and bringing to 650 - 900 degrees. The glass melts and becomes red-yellow in color, while the edges sintered with each other and with the glass base, forming a single whole. The fusion process is usually carried out at a temperature of 800 degrees;
- exposure - maintaining a certain temperature for some time, as a rule, maximum;
- cooling is a fairly quick stage. The temperature drops sharply to a level just above the annealing temperature. To achieve a strong decrease in temperature, just open the lid of the furnace;
- Annealing is the cooling of glass to a temperature equal to 580 degrees. At this stage, glass acquires its original shape and color;
- full cooling - cooling the product naturally to room temperature.
Fusing provides the ability to create multi-layer and embossed stained-glass windows without the use of metal broaches. Stained-glass windows made using the fusing technique have the extraordinary effect of a picture frozen in glass.
Sandblast
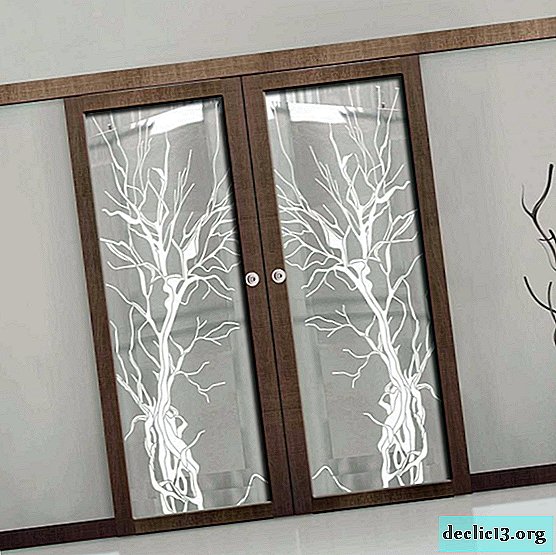
Peskostruy originated at the end of the 19th century, and is a technique for removing the upper layer of the glass surface using an abrasive consisting of a stream of a mixture of compressed air and pure quartz sand. Despite the seemingly simple simplicity, the technique requires certain skills and experience in handling equipment. Glass matting can be done both over the entire surface and with the help of a template that allows you to get a smooth pattern on a frosted surface and vice versa, a matte pattern on a smooth surface. Sandblasting can be done from two sides: from the front and from the back. In addition, it can be in-depth or superficial or even bilateral. The graininess of the applied pattern varies from very fine to coarse. Stages of glass sandblasting technology:
- selection and processing of the picture;
- stencil manufacturing;
- preparation of the base material (glass, plexiglass, mirrors);
- stencil fixation;
- surface treatment by feeding a mixture of compressed air with abrasive (quartz sand) under high pressure;
- applying a protective layer by applying a hydrophobic varnish.
There are several varieties of sandblasting:
- Flat sandblasting (frosting) is the simplest method of processing a glass surface with an abrasive, as It is based on drawing a drawing by a continuous method, without use of templates. Thus, the entire surface will be matted.
- In-depth sandblasting is a more complex technique, allowing deeper processing of individual elements of the picture. The technique requires the use of glass with a thickness of at least 5 mm
- The embossed sandblast is identical to the in-depth sandblasting technique. True, this method requires a glass thickness of at least 6 mm. It looks most impressive with the use of end lighting, which creates the illusion of a three-dimensional image. As an addition, engraving and neat relief are used.
- Art sandblasting differs by drawing a pattern not by a continuous method, but by intermittent matting. Due to this, tones and halftones are formed, which give the image realism, creating elegant transitions. Glass is suitable for any thickness, however, the work requires high precision and craftsmanship.
- Colored sandblasting can be obtained using a flat, in-depth or embossed pattern, followed by painting with a paint.
- Photo sandblasting is a completely new technology using digital photo printing, in which the quality of the initial result directly depends on the quality of the template.
- Double-sided sandblasting is a very complex technology in which the image is superimposed on both sides of the glass or mirror. It is very important that the drawings match perfectly, and the product has a neat appearance.
Painted stained glass
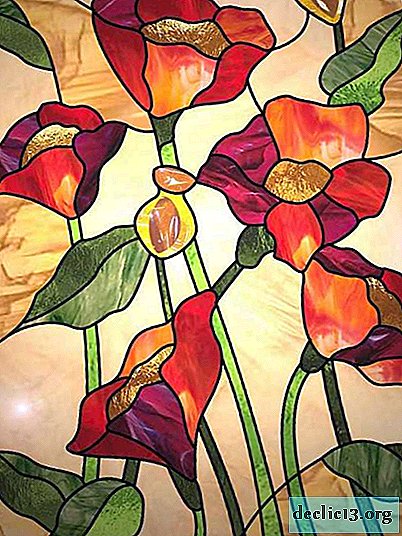
Painted stained-glass windows are the most popular and common types of pseudo-stained-glass windows, representing a glass manually painted with special paints. The process consists of several stages:
- creating a full-size sketch with dividing it into color fragments;
- Transferring the picture to glass: this happens by applying glass to the prepared sketch;
- drawing contours of the image with special contour paints;
- after the contour paint has completely dried, filling with stained-glass paints the corresponding colors of the glass fragments.
For painted stained glass, various types of paints are used - stained glass and firing paints, each of which has its own distinctive properties. Firing paints mean heat treatment after application to glass. Conventional stained glass paints are not subsequently fired. The painted stained-glass windows most resemble artistic glass paintings. Among other things, the painting technique allows you to create ready-made compositions in a wide variety of style solutions. The main feature of this technique is the special expressiveness, originality of the drawing and the aesthetics of manual labor.
Film Stained Glass
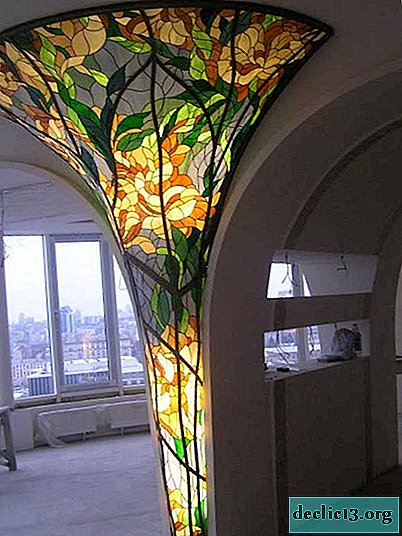
Film stained-glass windows are, first of all, low-cost equipment, which is one of the most modern ways to create pseudo-stained-glass windows, based on tinting glass with special special films with their further fixing along the contour with a tin or lead border. The main advantage of this technology is the use of flat glass. In addition to being convenient, it is also safe. In addition, such a stained-glass window has less weight and is perfectly flat. Film stained glass can be compared with an application where instead of traditional colored paper, polyester film is used. In this regard, it cannot be attributed to stained-glass windows as such, because this is most likely a high-quality imitation of a real stained-glass window, which includes several stages:
- sketch creation;
- drawing a pattern on glass;
- selection of contours using a special tape;
- filling the formed cells with a special film.
Due to the fact that when creating stained-glass windows, solid glass is used, the products are the most durable, which in turn allows us to produce large-sized stained-glass windows.
Fill Stained Glass
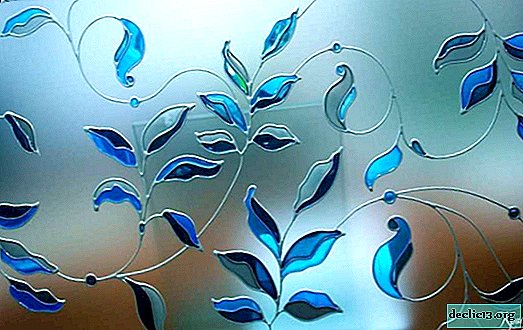
Fill stained-glass windows are a very popular technique based on the manual method. In this regard, the master stained glass artist is required to have a certain experience, as well as the artist’s talent, which will allow to achieve a high-quality imitation of the Tiffany technique. Quite often, this technique is confused with painting glass. Nevertheless, its main difference is the presence of a polymer relief contour that imitates a metal broach. The creation process also consists of several stages:
- creation of a sketch, in which all colors are subscribed, in full size;
- degreasing and dust removal of a surface;
- lining the sketch under the glass and drawing a contour of the picture with polymer paint;
- after the final drying, filling in the image elements with paints or varnish, according to the sketch;
- drying process within 24 hours.
This technology for creating stained-glass windows implies partial automation: the drawing of the future product is developed on a computer, after the polymer circuit is applied using special software-controlled equipment.
Fill stained-glass windows provide a huge selection of all kinds of drawings and patterns, they are safe, environmentally friendly and durable, as well as resistant to environmental influences.
Photo printing
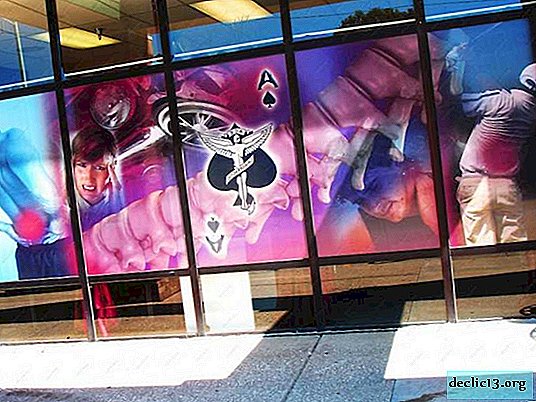
Photo printing on glass includes the general name of several different techniques for transferring images onto a hard surface. With the advent of this technique, the possibilities of designers in interior design have greatly expanded. The drawing can be printed both on a special film, which is subsequently glued to its surface, and on a solid basis. Accordingly, the first option is called direct printing, and the second - the manufacture of photo printing on glass. Each option has its own distinctive features. For example, sometimes a varnish or other basis for direct photo printing is applied to the surface, while both matte and transparent film can be used for printing on film.
Features of photo printing technologies:
- Direct photo printing - the image is printed on the glass surface of any texture and any size using a special printer. To create such a stained-glass window, special paints are used that can, under the influence of ultraviolet rays and high temperatures, penetrate deeply into the thickness of the glass and achieve high detail and brightness of the picture with the condition of the highest resolution.
- Film - is an overlay of a full color printing image on a film with its further gluing using polymer glue. Then, under the influence of ultraviolet light, the glue hardens, which contributes to a strong connection of the film image with glass.
- Triplex - this type of printing is based on the film method, where the drawing is also applied to a special film, then the finished photo is between two sheets of glass. It is the most reliable and durable photo printing method since The image is protected on both sides by glass.
The main advantages of the photo printing technique are the fast production time, as well as the ability to simulate classic stained-glass windows, environmental friendliness and relatively low cost.
Faceted Stained Glass
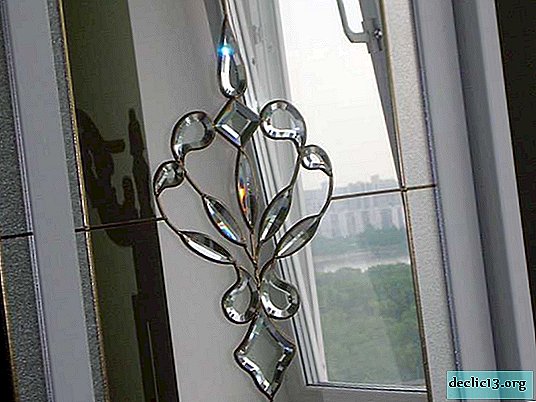
Faceted stained-glass windows represent an optimal technique in the case when it is necessary to emphasize a feature in the interior architecture, as well as a certain level of prosperity and the life of its owners. The unique ability of such a decor to refract in a special way both natural and artificial light forms a spectacular radiance similar to gems, such as a diamond. The technology for creating a facet stained-glass window is comparable with the classical one. The only difference is that all or several elements of the glass picture are processed in a special way in several stages:
- first, with the help of a special machine, an edge is cut from a glass surface at a certain angle;
- then it is polished, as a result of which it becomes dull and does not transmit light;
- the final stage is polishing, with which the part is made completely transparent.
To create stained-glass windows with facets, polished glass plates are usually used, having a thickness of 5 to 25 mm of various shapes, sizes and cut angles. When the need arises to enhance the effect of refraction of rays, a wider chamfer is removed, which requires glass having a greater thickness, which leads to an increase in the weight of the stained-glass window. Integrity of processing of elements and accuracy of assembly ensure a long service life of the product. Facet stained-glass window can also be made using rhinestones - glass volumetric elements with a facet. This decor is designed to decorate any surface made of glass. Rhinestones are fixed using special UV glue. As a result of this, the product has the greatest strength and light weight.
The main advantages of faceted stained-glass windows are structural strength, unusual visual effects, as well as durability.
Frosting glass
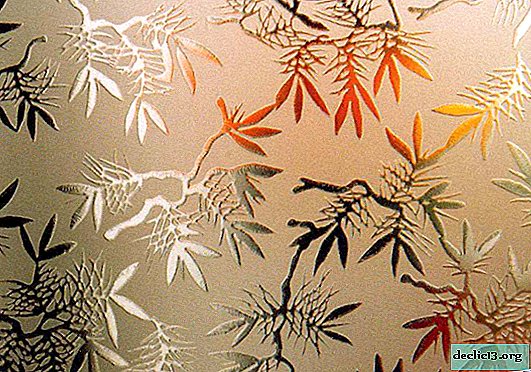
Glass frosting is a technique for processing the top surface layer, resulting in a matte pattern. Today, frosted glass can be made by machining, roasting technology, chemical etching, varnish coatings, art painting, as well as colored paint.
- machining - matting is carried out using sandblasting and engraving;
- chemical etching - a process that uses chemical reagents for frosting glass. A chemical reagent, acting on glass, destroys its surface layer. Reactive components include compositions with hydrofluoric acid (gels, pastes, aqueous solutions);
- firing technologies - matting technologies with firing in an oven are based on applying a special coating to the surface (firing stained glass paints) and then baking them in the oven, as a result of which the glass product acquires a rough surface at a certain temperature, and the image becomes a matte shade. Application of paints is done manually and implies strict adherence to the thickness of the ink layer;
- varnish and film technologies - a multi-colored stained-glass film is applied, applied on a flat or radius surface, and varnish coatings are also used. In case of breaking, the film does not allow the fragments to fly apart;
- painted method - glass matting is carried out using non-toxic stained-glass paints of two types: on water and solvent bases. The drawing is applied to the glass manually using a brush, stencil and contours;
- color matting - is carried out using colored polymer paints. First, a contour according to the sketch of the drawing is superimposed on the glass. Then, the contour cells are filled with colored enamels. Drying is carried out by air for several days or for several hours in a drying oven.
3D stained glass
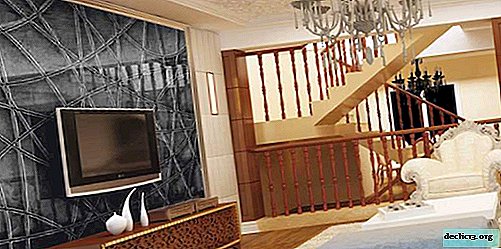
3D-stained-glass windows - are the latest technology that creates the illusion of a three-dimensional image viewed from both sides. In this regard, the technique is most often used for stained glass windows and consists of several stages:
- creating a sketch with a thorough drawing of all the details and a selection of suitable colors;
- cutting out each element of the glass picture, taking into account the sketch, as well as special processing: turning parts, removing chips and rough edges;
- assembly of a stained-glass window and connection of all elements into a single whole using brass solder;
- inserting a finished Tiffany stained glass window between two glass panes;
- high-temperature processing (850 degrees) of the product in a special furnace for 10 minutes;
- wrapping the cooled product around the entire perimeter with aluminum tape, as well as pouring liquid rubber on top.
The advantages of this technique are noise insulation, thermal insulation, impact resistance, safety, environmental friendliness, original appearance.
Combined
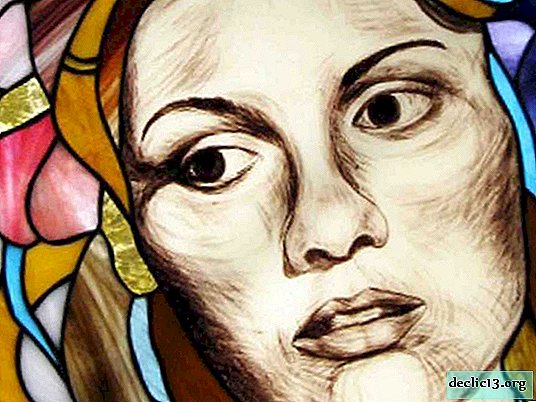
Combined stained-glass windows - are the most expressive and highly artistic products, because include several techniques that allows you to achieve unique results that cannot be repeated in the application of any one method of decorating a glass surface. For example, the Tiffany technique blends wonderfully with facet. Combined stained-glass windows are made exclusively by individual order and have a number of difficulties in view of using a combination of materials of different properties in the decoration of one glass product. But at the same time, this type of stained glass window represents the most interesting and peculiar among stained glass techniques. The combined stained-glass window manages to achieve an effect of three-dimensional (3D) image, extraordinary in its realism, of a special volume and depth.
Collages
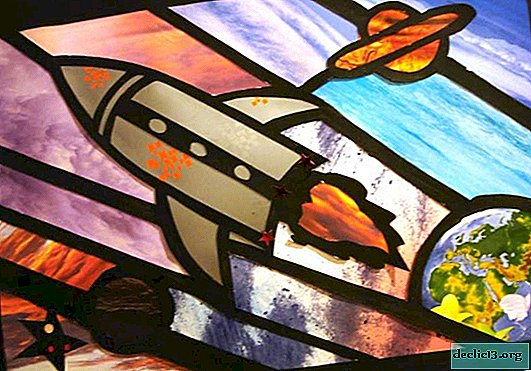
Stained-glass collages - represent a modern innovative technique, partly similar to the classic and Tiffany technique and also consisting of several stages:
- sketch design;
- cutting of multi-colored glass fragments;
- assembly of parts using a special polymer solution, the base of which (on which the assembly is carried out) is ordinary transparent glass.
The main feature of the stained-glass window-collage is considered to be the absence of clear lines of the pattern, due to which the composition is perceived as very light and transparent, where all the transitions are unusually smooth. Therefore, the design of stained glass-collages looks quite relaxed and natural, regardless of its location. A feature of the technology allows you to play absolutely any image.
Cast
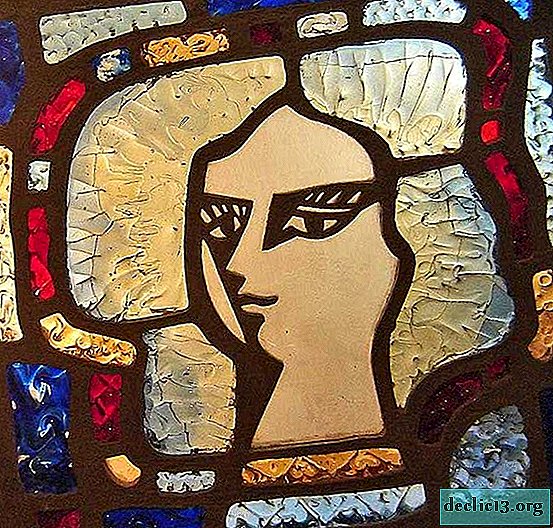
Cast stained-glass windows - a technique in which each glass module is either blown out or cast by hand. The thickness of the glass, which is given a surface texture that enhances expressiveness and refracts light, varies from 5 to 30 mm. To connect the glass, cement mortar and metal fittings are used.
The scope of each stained glass technique individually
Scope of application | |
---|---|
windows, mirrors, niches, paintings (panels), lamps, products | |
doors, partitions, niches, wardrobes, lamps, paintings (panels), mirrors, screens for batteries | |
doors, partitions, niches, wardrobes, paintings (panels) | |
windows, doors, partitions, wardrobes, mirrors, kitchen furniture | |
doors, partitions, windows, wardrobes, mirrors | |
Смотрите видео: Peter McGrain (April 2024). |